Lean in to workload management
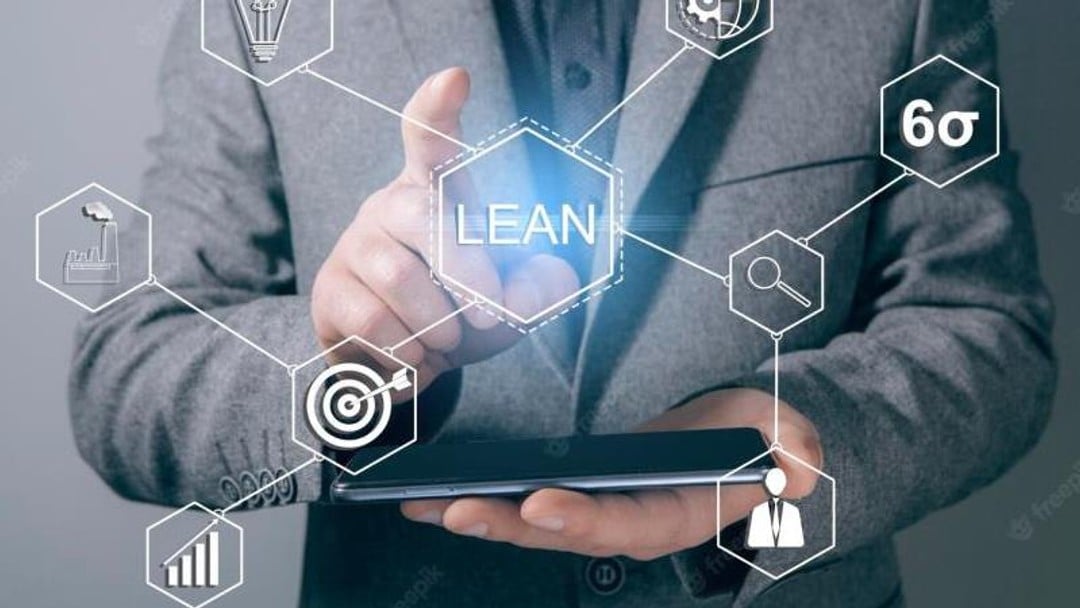
James Lancastle examines the benefits of Lean Six Sigma (LSS) for firms
“Why?” You ask, and your colleague replies: “I don’t know, but we’ve always done it this way.” Nearly all readers will have had this encounter in the workplace – it’s a pervasive theme in many organisational cultures.
We tend to complete tasks the way we’re told they’ve always been done, without questioning or revisiting the reason behind it, long after that reason ceases to exist. But this is how inefficiencies grow and become the norm – for example, time and work allocation is misappropriated, and bottlenecks continue to choke workflows.
What is LSS?
Businesses across multiple industries have applied the Lean Six Sigma (LSS) methodology. Through it, they have learnt operational processes that are unjustified and therefore inefficient (decision-making not based in fact or tangible benefit to their customer/client) don’t result in the value that equals or exceeds the expense spared.
Two complimentary process improvement approaches form the methodology of LSS, which targets quality improvement by identifying, answering and preventing problems. ‘Lean’ is a never-ending journey of seeking perfection which is built on respect for people and seeks to convert waste into value for the customer. ‘Six Sigma’ is data-driven, and aims to prevent defects or reduce variation. Together they create a lens and a philosophy through which you can assess and optimise efficiency within a business.
But firms have been slower at adopting this process improvement methodology, because of time and material charging rates being traditionally quite inflexible – and so this form of change management is still unfamiliar in the legal industry. But the urge from clients to provide more value while simultaneously reducing their costs is causing firms to assess their client service delivery for inefficiencies and reframe their working models so they can remain competitive. LSS can help them carry out this analysis, identify problems, and implement actions to resolve and prevent inefficiencies from occurring in future.
Below are two examples as to how LSS can be used in law firms to improve service delivery.
Case Study 1: the ‘5 whys’ in tackling ineffective work allocation
One of our firm client’s departments was struggling with inefficient, ineffective and unequal work allocation processes. Our first step was to clearly define the problem that was causing these issues, and then establish the boundaries of the investigation. We adopted the ‘5 whys’ analysis tool (a Lean technique) to identify the root cause of these issues, which were inevitably impacting the productivity of the team.
The ‘5 whys’ exercise originates from Toyota, one of the pioneers of Lean. The facilitator will ask the team “why?” as many times as necessary to identify the root cause(s) of a problem, to ensure informed action is taken to prevent it in future.
In our client’s case, a team of subject matter experts (a mix of junior and senior lawyers) was formed to participate in a 5 whys exercise, which was facilitated by a LSS practitioner, and uncovered more than one root cause.
Through this tool, we were able to identify the sources of the problems impacting their work allocation processes. This allowed for basic, yet highly effective, corrective measures to be identified – and action was taken to address the problem.
Case Study 2: the use of Value Stream Mapping (VSM) in addressing bottlenecks
Significant bottlenecks in the settlement agreement preparation process were impacting one of our other clients.
To identify what was and wasn’t adding value to our client’s service delivery, and therefore decide how we could dislodge the bottlenecks, it was necessary to perform VSM.
VSM was used to map the value chain efficiency of their settlement agreement preparation process, which was a cross-functional process involving two departments and our client. The value stream map enabled us to ‘see' the process and measure the current process performance based on several key performance metrics. All non-value added activities and waste were exposed – and their impact on process capability was quantified. The most significant defect was rework, which dramatically increased the process lead time, without adding any value for the client.
Countermeasures were then developed – and a future state value stream map was developed, which created a Lean process, improved FTR (First Time Right) – and increased the overall value chain efficiency.
Conclusion
As you can deduct from the above examples, LSS can be applied to optimise large and small inefficiencies within a firm and its departments. This change management methodology can ensure decision-making over processes is grounded in fact and/or data-driven, eradicating inefficiencies and ensuring value is delivered to clients.
James Lancastle is Lean Six Sigma analyst at Pinsent Masons Vario: pinsentmasons.com